Distillation: The Art of Separation & Purification
- Chemojo
- May 23, 2023
- 5 min read
Distillation is a widely used separation technique that plays a crucial role in various industries, including petroleum refining, chemical production, and the manufacturing of alcoholic beverages. It is a process that utilizes the differences in boiling points of substances to separate them based on their volatility. By subjecting a mixture to heat, vaporization occurs, and then the vapor is condensed back into a liquid state, resulting in the separation of different components. This article explores the principles, types, equipment, applications, advantages, and limitations of distillation, as well as its environmental impact and future trends.
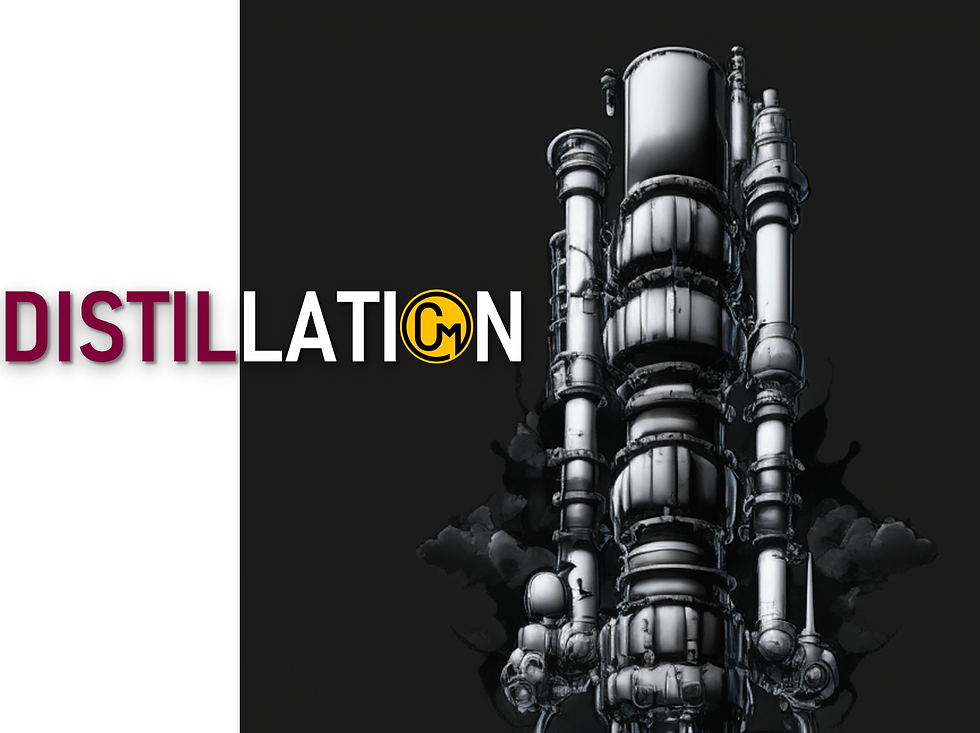
Definition of Distillation
Distillation is a fundamental process in which a liquid mixture is heated to generate vapor and then cooled to obtain a purified liquid product. This technique takes advantage of the fact that different substances have different boiling points. The components with lower boiling points vaporize more readily, while those with higher boiling points remain in the liquid phase. Distillation is widely employed in various industries due to its effectiveness in separating and purifying mixtures.
Basic Principles of Distillation
Distillation uses vaporization and condensation to separate liquid mixtures. Heat causes low-boiling point molecules to become gas, which is then cooled to become liquid again. The liquid collected is distillate, while the remaining liquid is residue.
Fractional distillation enhances separation with a fractionating column. Vapor rises, contacts liquid, and partially condenses. The condensed liquid flows down, enriching the vapor with lower-boiling components. This improves separation efficiency, especially for mixtures with close boiling points.
Types of Distillation
Simple Distillation
Simple distillation is the most basic type of distillation, and it is best suited for separating components with a wide range of boiling points. It entails heating the mixture and collecting the condensed vapour at a lower temperature.
Fractional Distillation
Fractional distillation is used when separating components with closer boiling points. The addition of a fractionating column provides better separation by allowing multiple vaporization-condensation cycles.
Vacuum Distillation
Vacuum distillation is performed under reduced pressure, which lowers the boiling points of substances. It is useful for separating heat-sensitive or high-boiling-point compounds.
Steam Distillation
Steam distillation is employed for extracting volatile compounds from heat-sensitive materials, such as essential oils. Steam is passed through the mixture, causing vaporization and subsequent condensation.
Azeotropic Distillation
Azeotropic distillation is used when a mixture forms an azeotrope, which is a constant boiling point mixture. Additional substances, known as entrainers, are added to break the azeotrope and enable separation.
Distillation Equipment and Components
Distillation Column
The distillation column is a vertical apparatus that provides a large surface area for vapor-liquid contact. It consists of trays or packing material that promotes the exchange of vapor and liquid, enhancing separation.
Condenser
The condenser is responsible for cooling the vapor, causing it to condense back into a liquid. Common types of condensers include shell-and-tube condensers and air-cooled condensers.
Reboiler
The reboiler is used to supply heat to the distillation column, promoting vaporization of the mixture. It can be a separate unit or integrated within the column.
Distillate and Residue Collectors
The distillate collector collects the purified liquid that condenses, while the residue collector gathers the remaining liquid after separation. These collectors ensure separate streams for the desired components.
Â
Â
Industrial Applications of Distillation
Distillation finds extensive use in various industries due to its ability to separate and purify different substances. Some notable applications include:
Petroleum Refining
Distillation is the primary process in petroleum refining, where crude oil is separated into fractions with different boiling points, such as gasoline, diesel, and lubricants.
Alcohol Production
Distillation is integral to the production of alcoholic beverages. It separates alcohol from fermented liquids, concentrating and purifying it to desired levels.
Essential Oil Extraction
Steam distillation is commonly used to extract essential oils from plant materials. The steam carries volatile compounds, which are then condensed to obtain concentrated essential oils.
Water Desalination
Distillation, particularly through methods like multi-stage flash distillation or multi-effect distillation, is employed in water desalination processes to obtain freshwater from seawater or brackish water sources.
Chemical Purification
Distillation plays a crucial role in purifying chemicals, such as solvents, by separating them from impurities and other byproducts.
Advantages and Limitations of Distillation
Distillation offers several advantages as a separation technique:
It is applicable to a wide range of substances, including liquids and mixtures.
It allows for the separation of components with relatively close boiling points using fractional distillation.
Distillation is a versatile process that can be scaled up for industrial applications or performed on a smaller scale in laboratory settings.
It is a physical separation method that does not require the addition of chemicals, making it environmentally friendly.
Distillation allows for the recovery and reuse of valuable components from waste streams.
However, there are certain limitations and challenges associated with distillation:
It can be energy-intensive, especially when separating components with similar boiling points or high boiling points.
Some compounds may be sensitive to heat and undergo degradation or decomposition during the distillation process.
Complex mixtures with azeotropic behavior may pose challenges in achieving complete separation.
Distillation may not be suitable for separating substances that form stable emulsions or have significant differences in volatility.
Environmental Impact and Sustainability Distillation processes can have environmental implications, primarily related to energy consumption and carbon emissions. The energy required for heating and vaporization contributes to the carbon footprint of distillation operations. However, efforts are being made to improve the sustainability of distillation processes:
Integration with Renewable Energy Sources: Incorporating renewable energy sources, such as solar or wind power, into distillation operations can reduce the reliance on fossil fuels and decrease carbon emissions.
Energy-Efficient Designs: Researchers and engineers are developing more energy-efficient distillation systems, such as heat-integrated distillation columns and advanced heat exchangers, to minimize energy consumption.
Process Optimization: By optimizing process parameters and employing advanced control strategies, the energy efficiency of distillation processes can be improved, reducing environmental impact.
Environmental Impact and Sustainability
As technology continues to advance, several trends and developments are shaping the future of distillation:
Advancements in Distillation Technology: Ongoing research aims to improve the efficiency and performance of distillation processes. Innovations include novel column designs, advanced packing materials, and enhanced heat transfer techniques.
Integration with Renewable Energy Sources: The integration of distillation processes with renewable energy sources, such as solar or geothermal energy, holds promise for reducing the environmental impact and increasing sustainability.
Membrane Distillation: Membrane distillation is an emerging technology that utilizes selective membranes to separate components based on their vapor pressure differences. It offers potential advantages in terms of energy efficiency and the ability to handle heat-sensitive materials.
Hybrid Separation Techniques: Combining distillation with other separation techniques, such as membrane separation, adsorption, or reactive distillation, can lead to more efficient and selective separations, opening up new possibilities for process optimization.
Conclusion
Distillation is a fundamental separation technique used in various industries for the purification and separation of substances based on their boiling points. It offers versatility, scalability, and the ability to separate components with high precision. However, it also has limitations, such as energy consumption and challenges with complex mixtures. The future of distillation lies in advancements in technology, integration with renewable energy sources, and the development of hybrid separation techniques. By addressing these challenges and embracing sustainable practices, distillation will continue to play a crucial role in industry while minimizing its environmental impact.
FAQs
What is the purpose of distillation?
Distillation is used to separate and purify components of a mixture based on their different boiling points, enabling the production of purified liquids or isolating specific substances.
How does fractional distillation work?
Fractional distillation uses a fractionating column to enhance separation. As the vapor rises through the column, it undergoes multiple vaporization-condensation cycles, resulting in better separation of components with closer boiling points.
Can distillation be used to separate mixtures with similar boiling points?
Yes, distillation can separate mixtures with similar boiling points, especially when employing fractional distillation techniques that utilize a fractionating column to enhance separation efficiency.
What is the role of a distillation column in the process?
The distillation column provides a large surface area for vapor-liquid contact, allowing for the separation of components based on their boiling points. It enhances separation efficiency by facilitating multiple vaporization-condensation cycles.
Is distillation a sustainable process?
Distillation can have environmental impacts due to energy consumption. However, efforts are being made to improve sustainability by integrating renewable energy sources, optimizing processes, and developing energy-efficient designs.
Thankyou!
#EnergyOptimization #ProcessDesign #ResourceUtilization #Sustainability #Safety #Productivity #Competitiveness #chemicalengineering #chemicalengineers
Comments